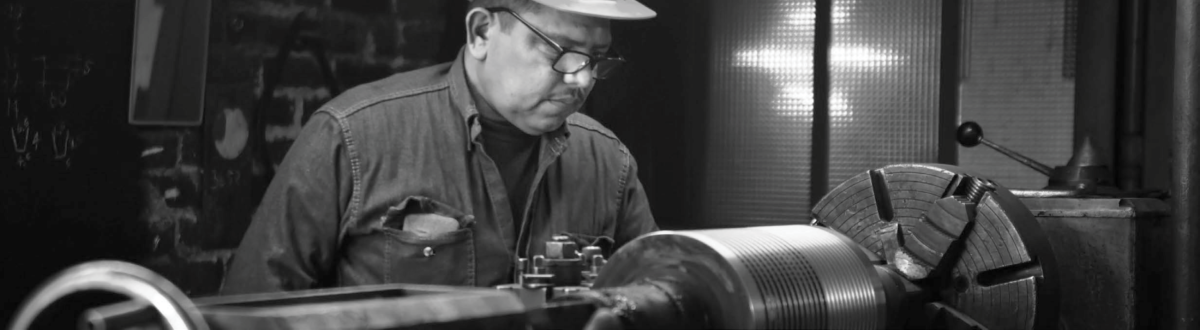
Case Study – Assembly Line
Q: Why are assembly line workers suffering so many injuries?
Our customer, a leading aerospace manufacturer of engines and components for commercial and military aircraft, was concerned about the high incidence of back and shoulder injuries on its assembly line. The company had spent significant sums of money on engineering redesign and injury claims, including the implementation of adjustable workstations where the majority of injuries were occurring. But none of these interventions was working. The company decided to use Senz™ motion sensing technology to identify the root causes of injury so corrective actions could be taken.
A: Adjusting behavior & workstations.
We assessed a cohort of workers at multiple workstations over a 65 hour period, using motion-tracking wearable sensors. Then we analyzed the data using our predictive analytics platform, Senz. The data showed that although the company had focused on the physical workspace, spending considerable sums to upgrade workstations, worker behavior had not been adequately addressed. Workers needed to be trained on proper body mechanics as well as on the set-up of adjustable workstations. Moreover, a key finding was previous intervention efforts were not sufficiently broad in scope.
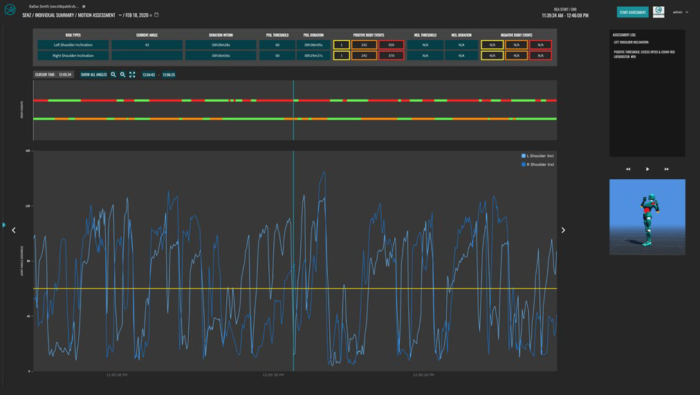
Outcome:
The data analytics revealed that the combination of behavioral and environmental factors was causing a higher repetition of awkward postures, putting workers at greater risk of shoulder and back strain. Additional training was provided to ensure workstations were optimized for each worker. After ergonomic and workstation trainings were completed and given time to normalize in regular operations, subsequent Senz assessments were conducted to quantify the success of the intervention strategy.
High Risk, Left Shoulder
- Total assessment time: 1 hr, 7 minutes
- Percent time in high risk: 73% left shoulder, 10% right shoulder
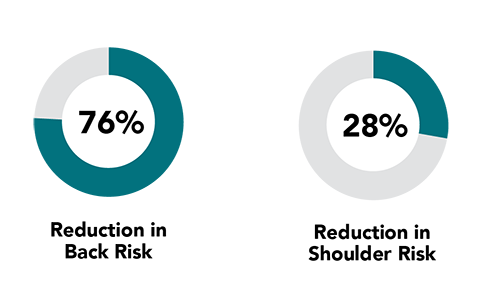
Join Our Mailing List