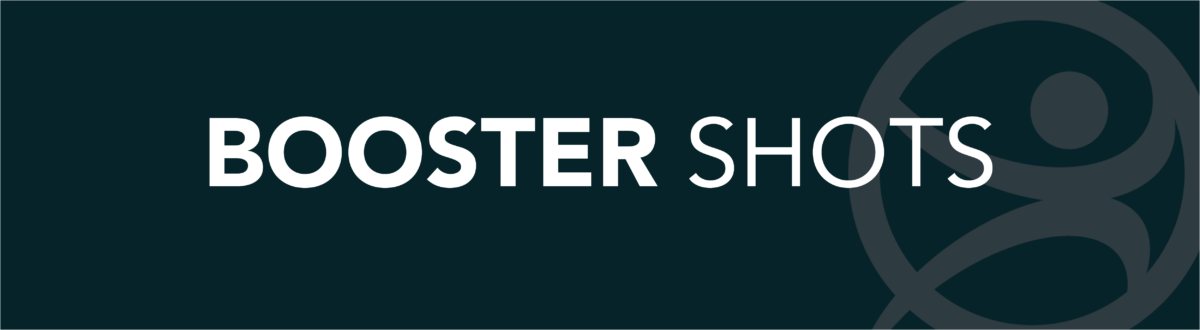
No 15 – Change Management Process
“While change is a driving force within organizations, it also presents challenges to health and safety teams as new processes and equipment mean changes to work hazards and the potential for employee injuries,” Join LifeBooster’s Program Manager & Ergonomist, William Thomas, as we discuss how organizations can analyze and account for risks proactively.
Are you looking to capture ergonomic risk factors as part of your change management process? Are you interested in eliminating ergonomic risks before they are ever introduced to your workforce? If you answered yes to either of these questions, then a wearables-enabled change management process is the right solution for you!
Failure to Consider Ergonomics in the Change Process Leads to Negative Downstream Risk Impacts on Workers
While change is a driving force within organizations, it also presents challenges to health and safety teams as new processes and equipment mean changes to work hazards and the potential for employee injuries. In particular, a failure to consider ergonomics early in the change management process can lead to negative impacts on employee health and safety and can increase musculoskeletal injury rates in your organization.
Wearables Provide a Fast and Effective Tool for Assessing Change Impacts Before and After a Change
A risk analytics platform and multi-point wearable system offers a solution to compare risk before and after a change has been implemented. Wearable sensors can be deployed to gain a baseline analysis of risk for an existing process, tool, or piece of equipment. From there, new changes can be implemented on a limited scale to provide a test environment to assess how risk factors compare to the pre-change process. Wearable sensors can then be re-deployed in this test environment to immediately quantify the change in the types and level of ergonomic risks from the existing to the new process.
Proactively Eliminating Ergonomic Risks Further Enhances the Cost Savings Expected from a Change
Based on this direct, apples-to-apples comparison of the current process and proposed change, your organization can identify impacts to musculoskeletal injury risk and can proactively account for and engineer out ergonomic risks. This saves significant costs in both downstream injury rates and in cost avoidance by preventing costly retroactive fixes after change has already been fully implemented.